Replacement process and scheme of RO reverse osmosis membrane in pure water equipment
2021-03-09
Part I: preparation
1.1 prepare all tools that may be used during construction
1.2 clean up the upstream water inlet pipeline;
1.3 carefully evaluate the quality of water inflow;
1.4 check whether the pipeline is leaking;
1.5 prepare water soluble lubricant (chemical pure glycerin);
1.6 ensure that all parts and chemicals used are complete;
1.7 check whether the pretreatment system operates and the water outlet is normal.
Part two: disassembly of old reverse osmosis membrane and installation of new membrane
2.1 disassemble the pressure vessel of reverse osmosis membrane, unify all end covers and parts and store them in sequence
2.2 take out the old RO membrane elements in the pressure vessel and wash the pressure vessel clean.
2.3 take out the new membrane element and check whether the position and direction of the brine sealing ring on the element are correct (the opening direction of the brine sealing ring must face the direction of water inlet).
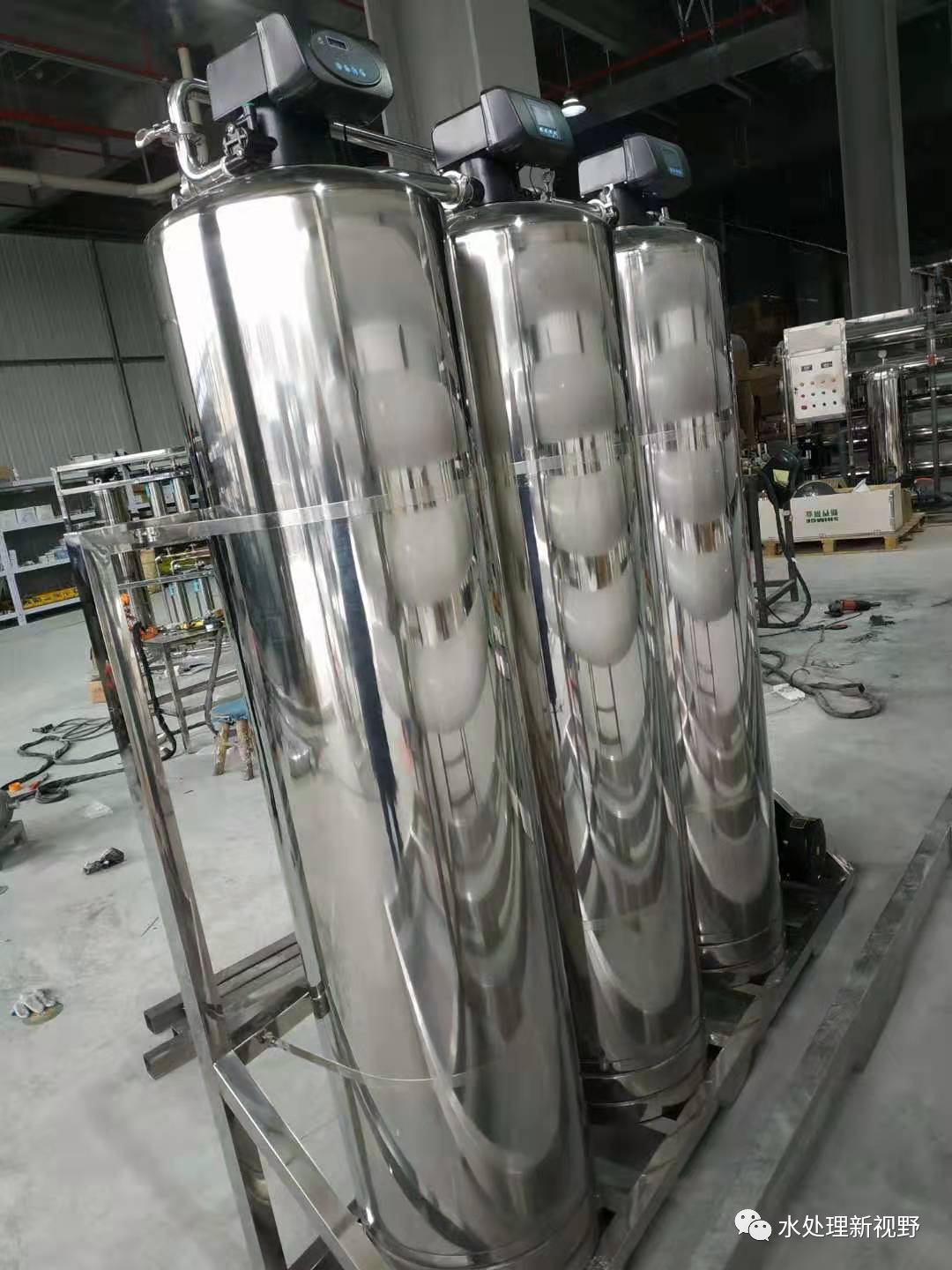
2.4 push the end of membrane element without brine sealing ring into the module shell parallel from the inlet end of pressure vessel until the element is exposed about 10 cm outside the inlet end of pressure vessel.
2.5 insert the connecting pipe between the components into the center pipe. Before installation, apply a small amount of glycerin lubricant on the "O" ring of the joint. If not, it can also be wetted directly with qualified pretreatment water.
2.6 take out the second membrane element, check whether the position and direction of the brine sealing ring on the element are correct, hold the element and let the connecting pipe on the first component insert into the center pipe of the element, push the element into the pressure vessel in parallel until the second element is exposed about 10 cm outside.
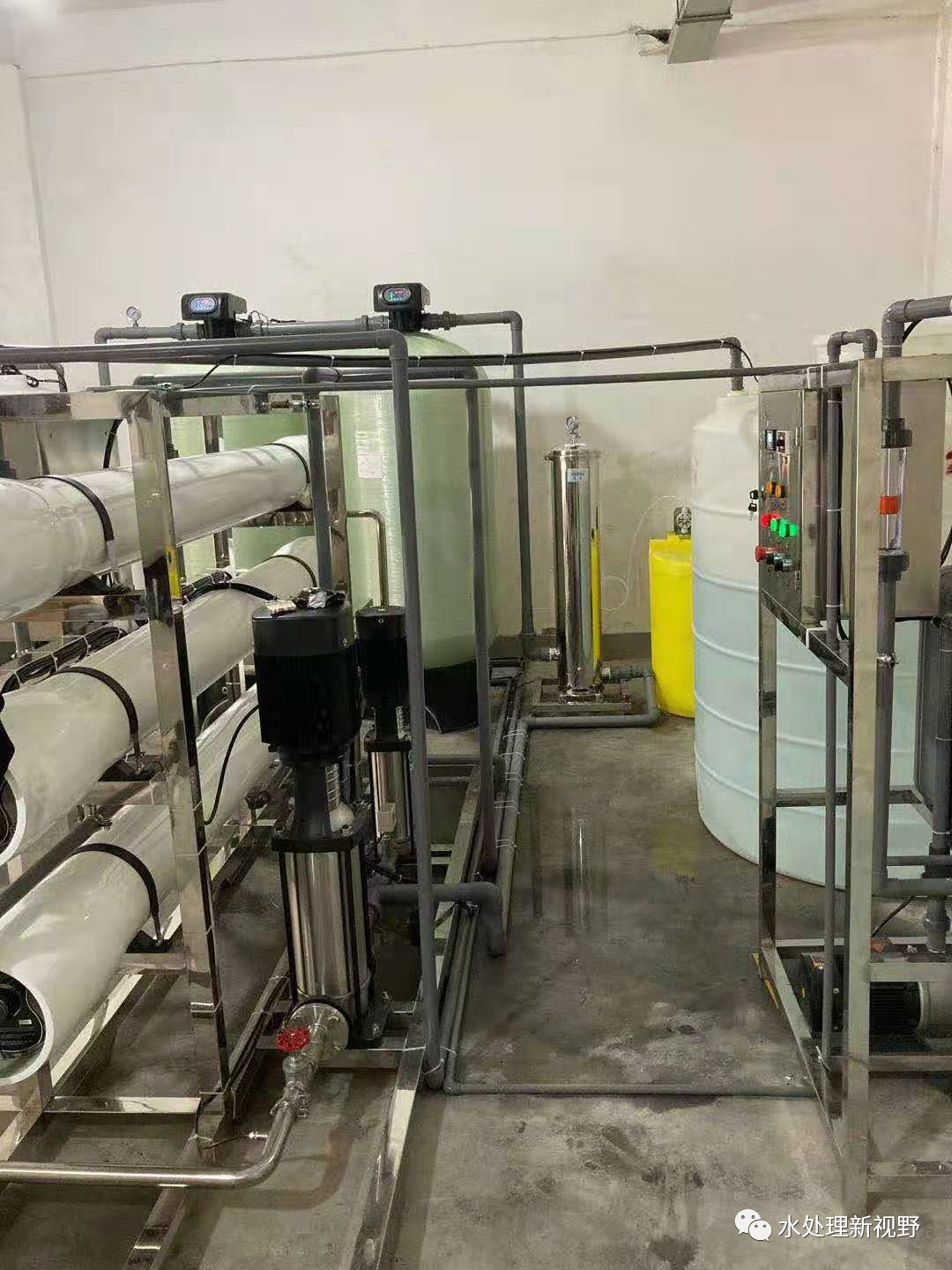
2.7. Repeat the steps until all components are installed in the pressure vessel, transfer to the concentrated water end, and install the connecting pipe on the center pipe of the first component. The length of the components and pressure vessels determines the number of membrane elements that can be installed in a single pressure vessel. During installation, install thrust ring at the concentrated water end of the pressure vessel.
2.8. check the "O" ring on the element adapter, insert the element adapter into the concentrated water end plate, align the component connecting pipe, push the concentrated water end plate assembly into the pressure vessel in parallel; rotate and adjust the concentrated water end plate assembly to align it with the external connecting pipe; install the end plate circlip
2.9 push the membrane element from the inlet side to the concentrated water side until the first installed membrane element contacts the concentrated water end plate firmly.
2.10. Install the water inlet end plate. Before installing the water inlet end plate, in order to prevent the axial movement of the components during the system startup and shutdown and the impact between the components, the gap between the membrane element and the end plate can be adjusted by adjusting plate (5mm thick).
2.11 repeat the above steps, install membrane elements in each pressure vessel and connect all external water inlet, concentrated water and water production pipelines.
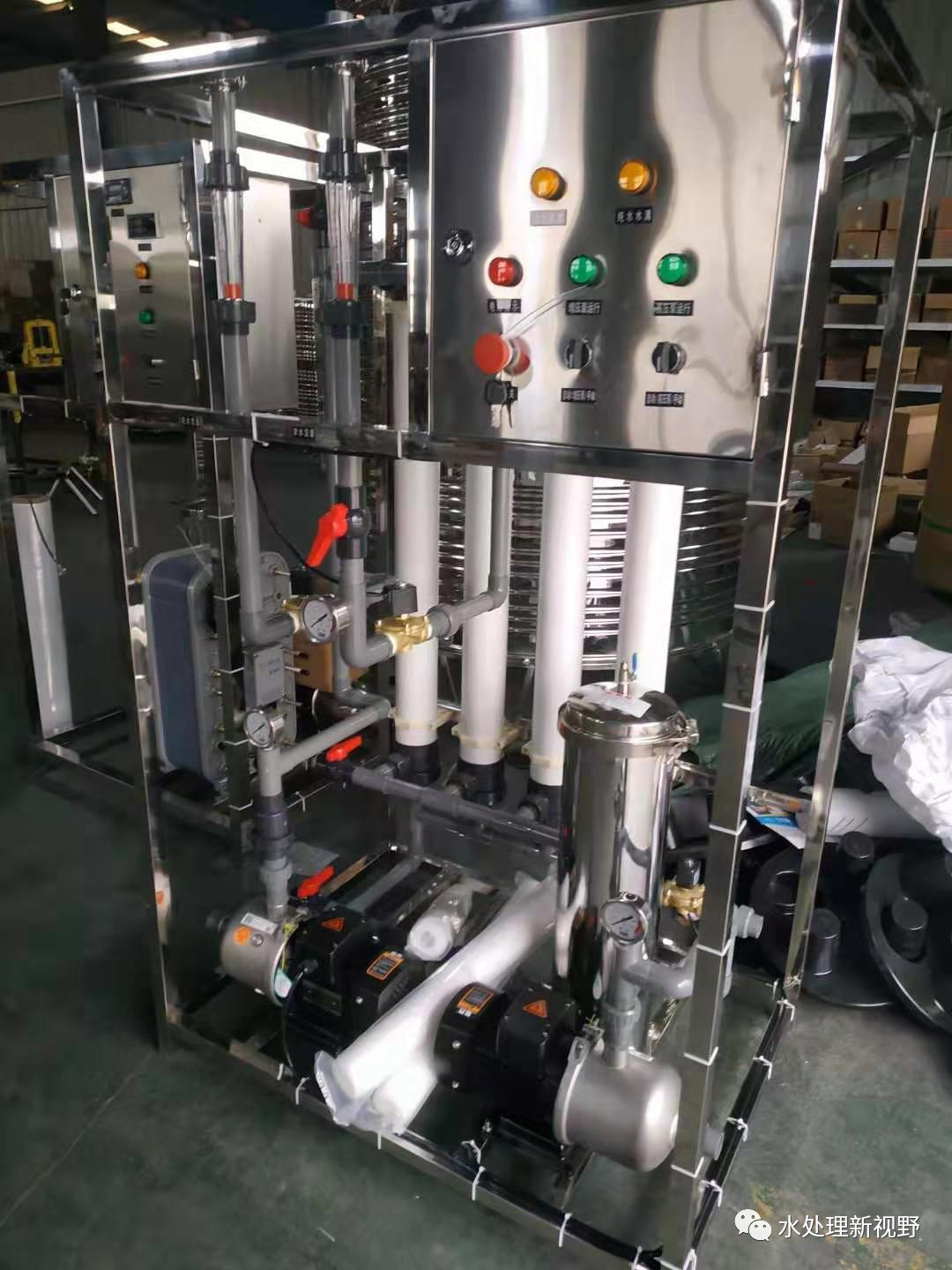
Part three: equipment commissioning
3.1 inspection and preparation before commissioning, including the following parts:
1. configure measuring instruments to correct all instruments;
2. set sampling points of all links of the system, and set interlocking, delay and alarm devices correctly;
3. check the connection between pressure vessel and cleaning pipeline, and fasten all joints;
4. the idle load test run of all rotating equipment such as water pump shall ensure correct steering and good lubrication;
5. open the water production discharge valve and the concentrated water discharge valve;
6. before starting the high-pressure pump, adjust the opening of the outlet valve of the high-pressure pump, and control the water inflow flow of the membrane system to be less than 50% of the water inflow in the operation operation.
3.2 check all valves and ensure all settings are correct. The water producing discharge valve, water inlet control valve and concentrated water control valve of membrane system must be fully opened.
3.3. Use low pressure and low flow qualified pretreatment water to drive out the air in membrane element and pressure vessel. All produced water and concentrated water in the process shall be drained to the sewer.
3.4. During flushing operation, check whether there is leakage point at the connection of all valves and pipelines.
3.5 for dry film system, it shall be washed continuously for 6 hours or 1-2 hours at low pressure continuously, and then washed for about 1 hour after overnight immersion. During low pressure and low flow flushing, scale inhibitor is not allowed to be added to the pretreatment part.
3.6. confirm again that the water production valve and concentrated water control valve are in the open position.
3.7 the first startup of high-pressure pump must be in a state where the water inlet control valve between the high-pressure pump and membrane element is close to full close, so as to prevent the impact of water flow and water pressure on membrane elements.
3.8 start the high-pressure pump.
3.9 avoid overpressure impact on membrane system. After the high-pressure pump is started, slowly open the inlet water control valve at the outlet of high-pressure pump to increase the concentrated water flow to the design value evenly, and the pressure-up rate shall be lower than 0.07 MPa per second.
3.10. While slowly opening the inlet water control valve at the outlet of high-pressure pump, slowly close the concentrated water control valve to maintain the discharge flow of concentrated water specified in the system design, observe the water production flow of the system, and gradually adjust to make the recovery rate reach the design value.
3.11 check whether the dosage of all chemicals is consistent with the design value, and determine the pH value of the water inlet.
3.12. The system runs continuously for 1 hour. When the water production is qualified, open the qualified water delivery valve and then close the discharge valve of the production water to supply water to the subsequent equipment. Record all the first set of operating parameters. The above-mentioned adjustment is generally carried out in manual operation mode, and the system will be converted into automatic operation mode after stability.
3.13 after 24-48 hours of continuous operation, check all recorded system performance data, including inlet pressure, pressure difference, temperature, flow rate, recovery rate and conductivity. At the same time, sampling and analysis of water inflow, concentrated water and total system water production. Confirm that the equipment is in normal operation and the construction is completed.